Checklist for connectors & cable assemblies
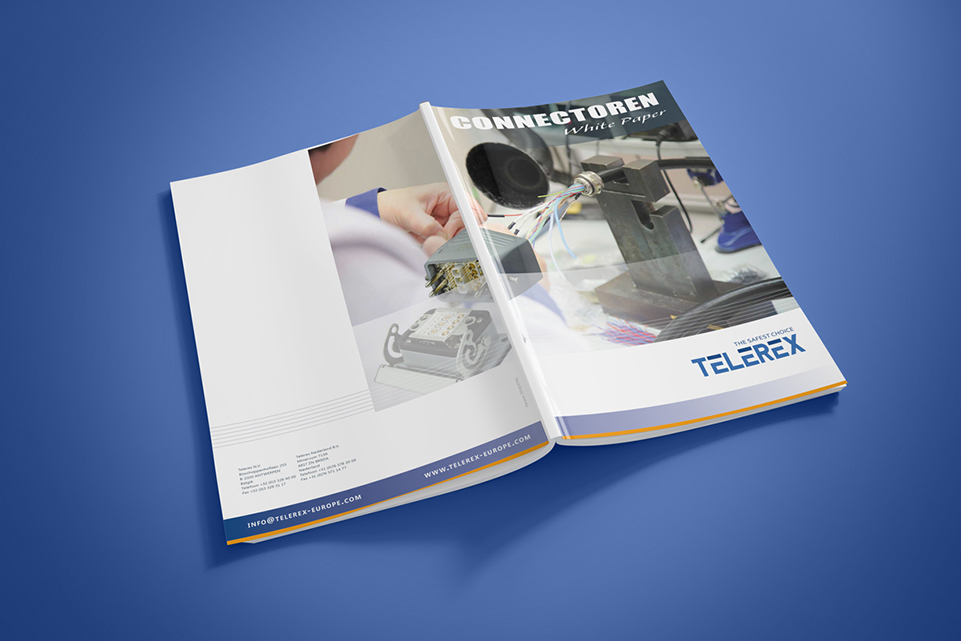
12 questions for the selection of a connector or cable assembly
Would you like to download the complete whitepaper?
There are few applications that can function without some form of interconnection. Whether it is medical equipment, industrial machines, or military gear, they all need connectors for power supply or transmitting electrical signals. However, the type of connector varies greatly depending on the application. What should you consider when selecting a connector? And what is needed for a good attachment of the connector to the cable? In this whitepaper, we seek answers to these and other questions.
WHAT IS A CONNECTOR?
A connector enables an electrical connection that can also be easily disconnected. This can be an internal connection between components in a machine or outgoing to connect devices to each other. For a good and safe connection, a connector always consists of two parts, a male and a female part. The female part provides voltage, signals, or both. The male part is almost always attached to a cable and is the part that receives the voltage or signals.
VARIOUS TYPES OF CONNECTORS
Connectors come in many different types and sizes. There are connectors made of metal and plastic, with different connection forms, that only transmit power or only signals, variants that are waterproof, etc. There are also connectors that are particularly suitable for medical applications, industrial use, or military applications. Examples of the above connectors include:
Loose lamella and wire spring contacts
These are contacts with a diameter of 0.76 to 50 millimeters suitable for numerous applications, such as assembling a docking system. Wire spring contacts can handle currents up to 2000 amperes.
Round (circular) connectors
Round connectors are used for test and measurement equipment, data traffic, voltage cables for low or high power, and even the transmission of gases or liquids. The forms are as diverse as the applications.
Push-pull connectors
This is a standalone category within round connectors. Push-pull connectors have a locking mechanism that automatically 'clicks' when the connector is inserted. Disconnecting can only be done by sliding the shell or housing of the connector backward. The connection does not break by pulling on the cable. This feature makes push-pull connectors very suitable for medical equipment, test and measurement systems, sensor technology, or critical military applications.
Board-to-board connectors
This type of connector is intended for high-speed, high-density, and high-power applications. Think of stacking or connecting circuit boards at different angles.
LED connectors
This emerging category is intended for connecting LED applications. Think of round and waterproof models with diameters of 10 to 25 millimeters. The connectors are available with 2 to 14 contacts and can handle up to 30 amperes per contact.
VARIOUS ASSEMBLY POSSIBILITIES
Not only is the range of connectors very diverse, but the possibilities for attaching a connector to a cable also vary widely. Will you crimp, solder, shrink, or screw the contacts? Is a Hot Melt (encapsulation) needed to make the connection waterproof? And should the assembly take into account heavy tensile forces on the cable and connector?
These are considerations that are often made too late in the development process of a machine. And then it turns out, for example, that the selected cables are too thick for the intended connectors, the right equipment for assembly is not available, or the connectors have a much longer delivery time than hoped.
CHECKLIST
Setbacks such as the lack of proper assembly equipment and long delivery times can have far-reaching consequences. For example, a late delivery of a machine can result in 'downtime penalties' for the machine builder. With careless assembly, you risk short circuits, electric shocks, or even fire. The desired certification of a system can also be jeopardized if the cable assemblies do not meet the requirements. Such adverse consequences can be avoided by critically looking at the required connectors and cable assemblies during the design of a machine. Below is a checklist of important questions.
1. WHAT CAN THE SOLUTION COST?
This is an important consideration. By answering this question, several options are immediately eliminated. There are large price differences between connectors. The intended quality and durability often play a significant role in the consideration.
2. WHAT IS BEING CONNECTED?
Are you connecting sensors, for example? And how many? Are the connectors intended for transmitting only signals or only power? Is the connector mounted on a coaxial cable? This basic information is needed to select the right connector and then the right assembly method.
3. WHAT TYPE OF CABLING IS SELECTED?
Is the cabling already selected? Or is a sensor being connected that already has a cable attached? Then the specifications of the cable – such as thickness, construction, and number of cable cores – partly determine the choice of the connector. For a thick cable, several connectors are eliminated due to the attachment method.
4. WHAT WILL BE THE LOCATION OF THE CONNECTOR?
Is the space for a connector limited? Then this must be taken into account when selecting the connector. A direct connection to the circuit board ensures, for example, that the circuit board must always be placed along the housing. This limits the freedom of choice.
5. WHAT ARE THE ENVIRONMENTAL FACTORS?
Will the machine be in a humid environment or are there very high temperatures? Then it is advisable to select a connector that can handle these conditions. If working in explosive environments, an Ɛx certification may be required under the ATEX 114 directive. Is there a chance of electromagnetic radiation in the environment? Then a metal connector with a shielded cable is the best option.
6. HOW ROBUST MUST THE SOLUTION BE?
Does a heavy cable cause a large tensile force on the connector? Then a strain relief for the transition from cable to connector is needed to prevent a break at the attachment. An alternative is a harder cable that relieves the connection, such as 'Drag Chain' cables. It is also good to know how often a connector is disconnected. Is a system intended to test other machines? Then choose a connector suitable for a large number of 'mating cycles.'
7. IS A HOT MELT NEEDED?
Connections between the connector and cable are encapsulated with hot melt glue to hide the applied technology, bridge a thickness difference between cable and connector, or make the connection waterproof. The shape of an encapsulation can also be personalized and provided with a logo. Consider the investment in a mold and selecting a good partner for the production process, as applying Hot Melt is very specialized work.
8. ARE THERE CERTIFICATION REQUIREMENTS?
Does a machine need to obtain a CE (Conformité Européenne) marking indicating that the product meets legal requirements? Or is a UL (Underwriters Laboratories) certification required for export to the United States or Canada? Then the connectors and cable assemblies must also meet the requirements arising from the certifications. Proper assembly according to the standards of the Institute for Printed Circuits (IPC) certainly helps with this.
9. IS THE RIGHT ASSEMBLY EQUIPMENT AVAILABLE?
Increasingly, the cable part is not attached to the connector with solder contacts but with crimp contacts. Special and expensive assembly equipment is needed for this attachment. It may be worth considering outsourcing the assembly to a specialist party that already has the necessary assembly equipment.
10. CAN I TEST THE CABLE ASSEMBLIES?
After assembly, you want to be sure that the crimps are properly placed, that the connection between the connector and cable is strong enough, and that the Hot Melt really keeps water out. To find this out, you need to subject the cable assemblies to various tests with special test equipment.
11. DO I HAVE THE RIGHT PEOPLE?
Assembling connectors can be a time-consuming task and requires a certain skill. It helps, for example, to choose one 'family' of connectors from the same manufacturer that your assemblers have experience with. Alternatively, you can outsource the assembly to a specialist. Your engineers will then have more time to further develop and perfect the systems.
12. ARE ALL NECESSITIES DELIVERABLE ON TIME?
A good cable assembly depends on the availability of the right components and assembly equipment and the presence of knowledge and experience. At an early stage of the development of a machine, check whether all components can be delivered on time. A late delivery of a machine due to (unexpectedly) long delivery times can result in penalties for the machine builder. It is then wiser to have the assembly carried out by another party.
MODULAR CONNECTORS
In this document, we have mainly discussed regular connectors and cable assemblies, but we do not want to leave an important product group and its possibilities unmentioned. We are talking about modular connectors, with which an infinite number of variations can be assembled.
This is not only about variations in shape and size but especially about the possible combinations of connector modules. These modular connectors can contain a combination of power, low current, compressed air, fluids, high-speed data, and much more.
Housing and locking can be adjusted to the application, usage requirements, ranging from 10,000 to 100,000 mating cycles. With these modular connectors, all conceivable cable assemblies can be built. Due to the versatile nature of these connectors, this is really specialized work.
OUTSOURCING CONNECTORS & CABLE ASSEMBLIES
If you choose to outsource the cable assembly, select the executing party with care. It may be preferable for the assembly to take place in Europe or even in the Netherlands. Does the intended party have a broad portfolio, the right assembly equipment, and test equipment? From certifications, it may also be a requirement that the work is carried out according to IPC standards.
Telerex supplies a wide range of connectors and can also take care of the assembly. Together with the customer, we determine exactly what is needed. We then purchase the connectors, take care of the assembly, and deliver the requested solution at the right time. Only then will you receive the invoice. An advance investment is therefore not necessary.
If you would like to know more about our offer in the field of 'connectors & cable assemblies', please feel free to contact us.
Author: Raymond van Spall, Account Manager Connectors & Cable Assemblies